Daylight Homeless Center: A Sustainable Shipping Container Shelter Designed by Forsite Studio
Forsite Studio’s design for the Daylight Homeless Center in Austin transforms a vacant big-box store into a vibrant shipping container shelter, addressing the urgent need for affordable, durable housing. By utilizing prefabricated cargo containers as micro living units, the project offers both cost-effective and flexible solutions while maintaining high standards of safety and sustainability.
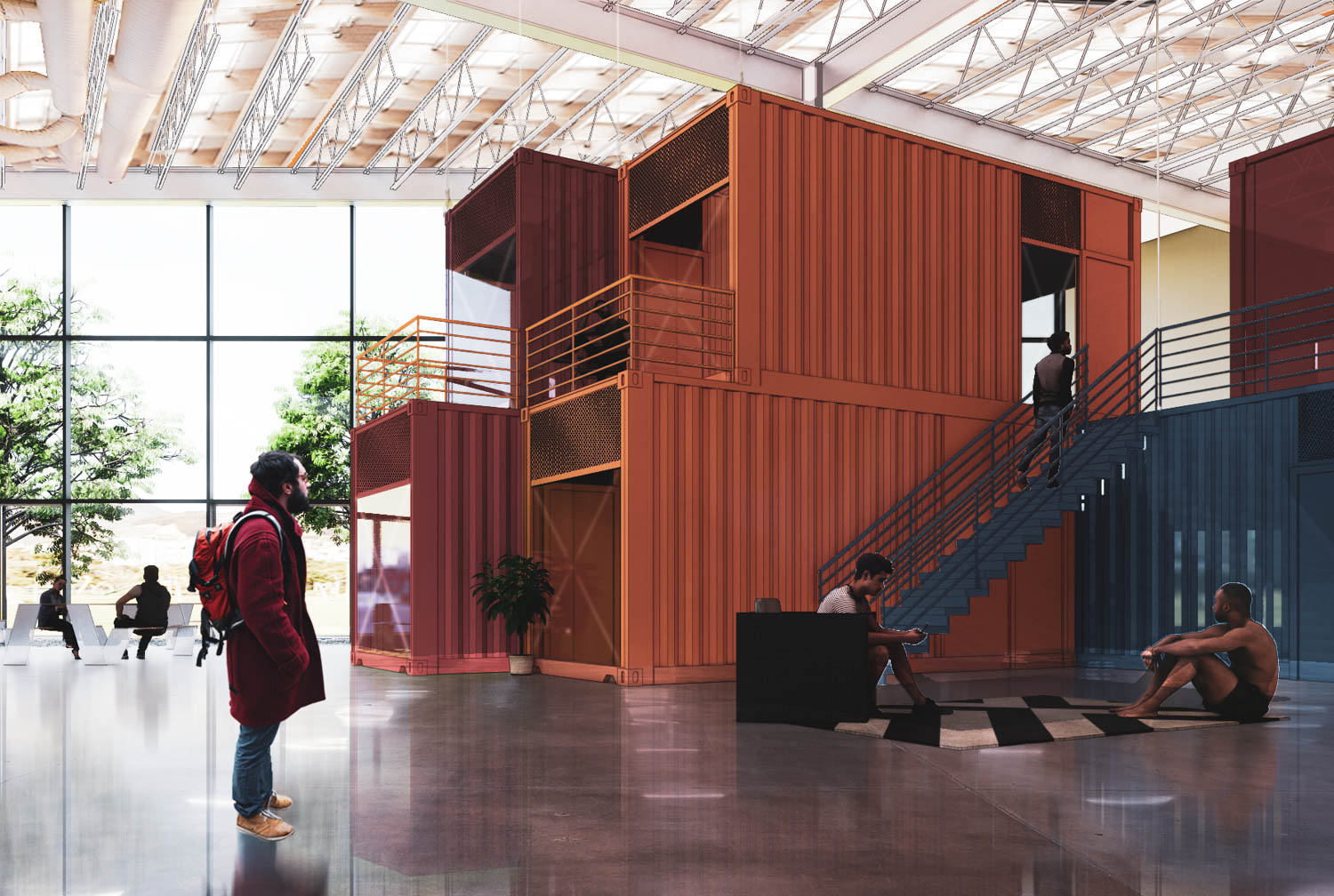
The adaptive reuse approach integrates communal spaces and strengthens connections to the adjacent Saint Johns Park, creating a shelter that fosters a sense of community and provides long-term stability for its residents.
Interview text by Dan Loe of Forsite, Imagery by Forsite Studio, Published with Bowerbird
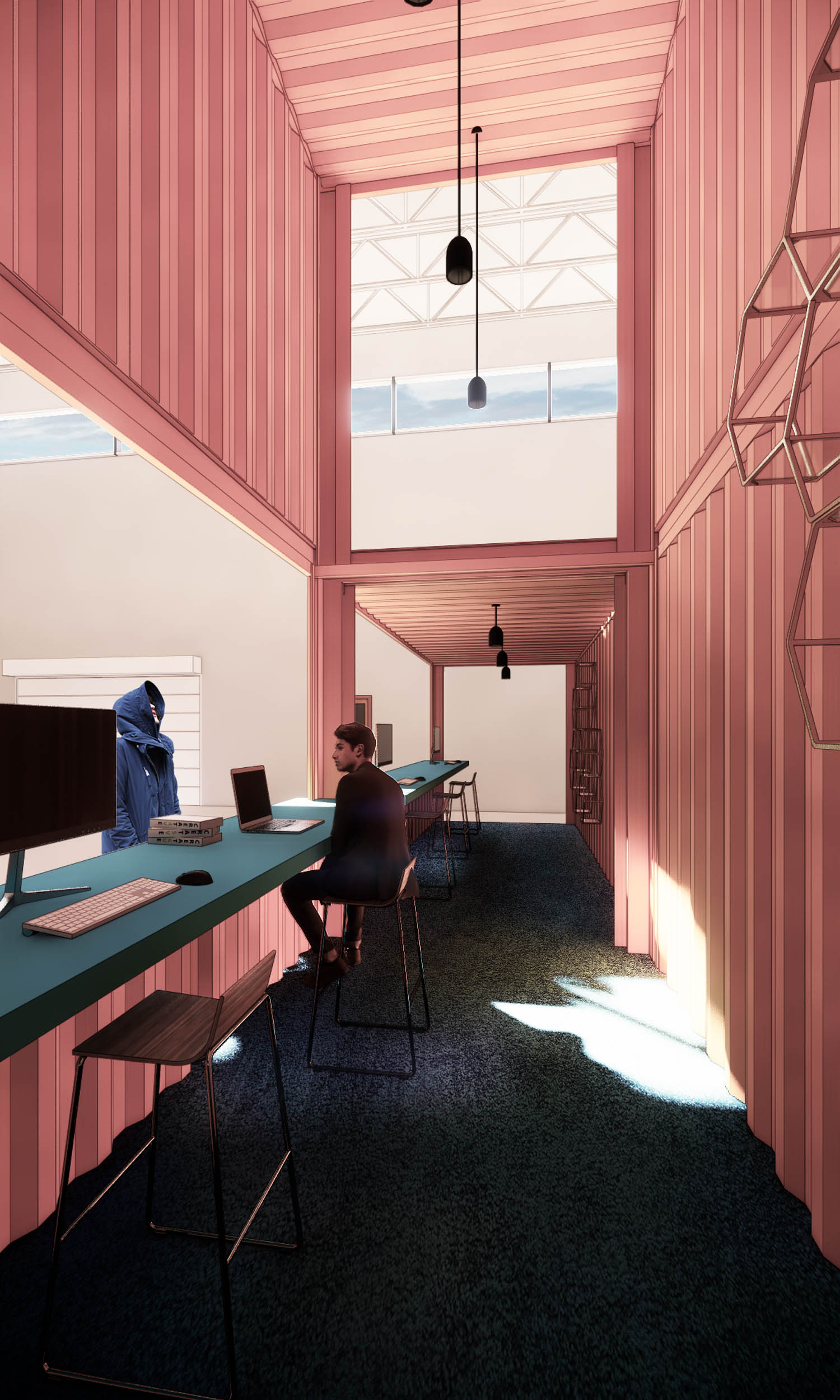
Could you share some background on Forsite Studio and your overall design philosophy?
Forsite is an architecture firm with construction capabilities. Based in Austin, TX since 2007, our operations have recently expanded to Central America.
Our philosophy starts with the belief that the most sustainable material is the one not used. To that end, we believe in unitization and standardization. This process involves taking units of material i.e. 2×4 lumber, steel W sections and creating standardized assemblies that can be easily repeated to generate form. Using our creativity within these parameters results in an efficient construction duration, limits waste and reduces build costs.
We believe in site specific architecture and using local materials and local craftsman to give meaning to structures we build.
How does your approach align with the needs of adaptive reuse projects like the Daylight Homeless Centre?
We started by repurposing the existing vacant big box store that had sat vacant for a decade. We chose to modify it in such a way that it would respond to the unique local site conditions, specifically it would open up to the community park directly behind it. In doing so, it would cease to be the ubiquitous big box structure indifferent to its surroundings.
Secondly, we utilized standard cargo containers and stacked them to create smaller, more intimate spaces within the larger community.
Forsite Studio’s design for the Daylight Homeless Centre uses prefabricated cargo containers for micro living units. What advantages did you find in using prefabricated elements for this adaptive reuse project, particularly in terms of cost, speed of construction, and flexibility?
Unless one is willing to pay a premium for the container aesthetic, usually it doesn’t make fiscal sense to repurpose cargo containers as a means of achieving cost effective construction. Efforts required to adapt the metal containers for habitable use outweigh the costs of building new with wood. However, in this instance, because the existing big box structure is providing the building envelope, there are very little modifications required to the containers. The building code will require modifications to the doors in order to provide access, but otherwise, these will be cost effective and safe living/sleeping pods within the larger center. The containers provide durability, flexibility and security that couldn’t be achieved with the typical wood framing and gypsum construction.
With regards to flexibility, depending on tenant needs, the pods can be reconfigured within the larger structure with moderate effort. Each pod can be moved with a lift, restacked to a new position and plugged into the electrical grid. Future expansion by adding more containers is also relatively simple and cost effective.
Prefabrication allows for more control over the construction process. How did using prefabricated units help ensure the durability, safety, and efficiency of the Shipping Container Shelter, given its focus on long-term stability for residents?
The containers are basically indestructible, which is great as long as they don’t need to be modified as discussed previously. They have a Class A fire rating – extremely important in this environment. Operating budgets for comparable facilities generally have significant line items for maintenance and upkeep. However for the pods, there’s very little maintenance required, they’re painted as needed and can be easily cleaned with a power washer.
In our research leading up to the project, we learned that many individuals experiencing homelessness, have to relearn how to inhabit and maintain their own spaces. For example, taking someone living on the streets and putting them in an apartment is not likely to result in a successful transition. The durability of the containers allows these pods to be an intermediary step on this transitional path.

The design incorporates verdant communal spaces and ample natural light. How does prefabrication support the integration of these elements into the living environment, and what role does this play in improving the residents’ quality of life?
There’s a quality of light and a subsequent quality of life that all too frequently community driven projects like this are lacking. As architects, we know items like skylights, interior planters and vegetation are some of the first things to be value engineered, (cut), so we wanted to be very strategic about how funds were spent.
As builders we understand construction costs better than most architects. We wanted to limit what was site-built because these unique one-of-a-kind installations are more susceptible to price fluctuations and schedule overruns. By repurposing an existing structure and using standard containers for living units it allows us to incorporate more amenities that would normally be cut in a project of similar complexity.
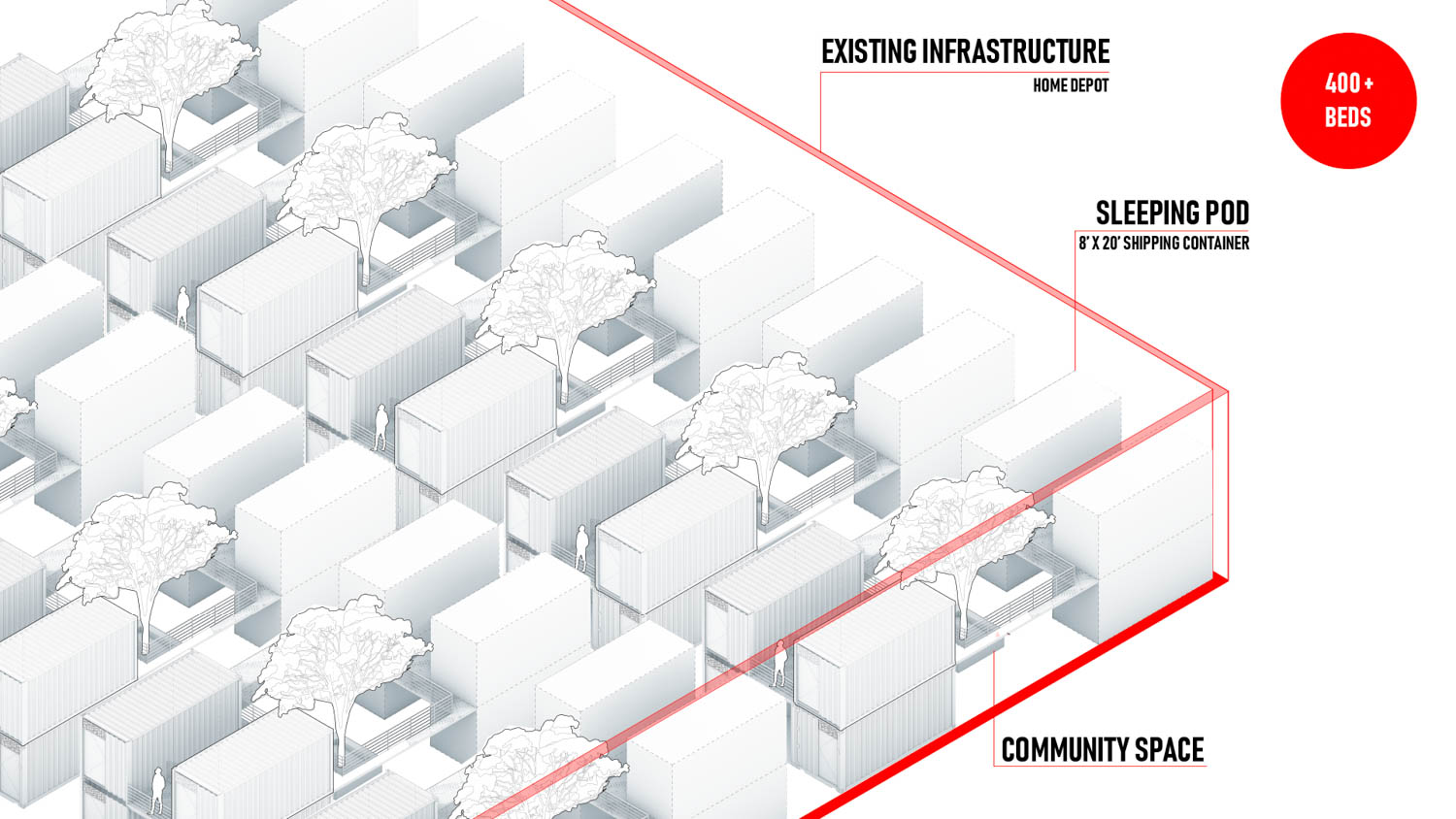
The anticipated cost per Shipping Container Shelter is $12,000, making this project a highly cost-effective solution for addressing homelessness. Could you explain how prefabrication and modular construction contribute to achieving such an economical result while maintaining quality?
We’re capitalizing on the economy of scale used in mass production of the containers. We’re able to keep costs low because we’re doing very little customization to the units.
The modularity of the units also allows us to achieve tighter tolerances. The machine made units are simply placed on top of each other and locked into place.
From a construction standpoint, time is money. The more complex a project, the higher the construction cost. Modular construction, on the other hand, is relatively simple. A standardized unit is systematically and repeatedly placed. A modular project can be completed on a relatively fast timeline.

Forsite Studio’s design also includes a range of support services on site, like medical clinics and skill training. How did prefabrication play a role in accommodating these diverse needs within the overall layout of the Daylight Homeless Centre?
The support services utilize containers to create ‘rooms’ within the larger center. While these support spaces would require more customization than the living units, the increasing popularity of modular construction and specifically, container construction, allows these to still be off-the-shelf products. Known costs and timelines are paramount on projects of this size and complexity.
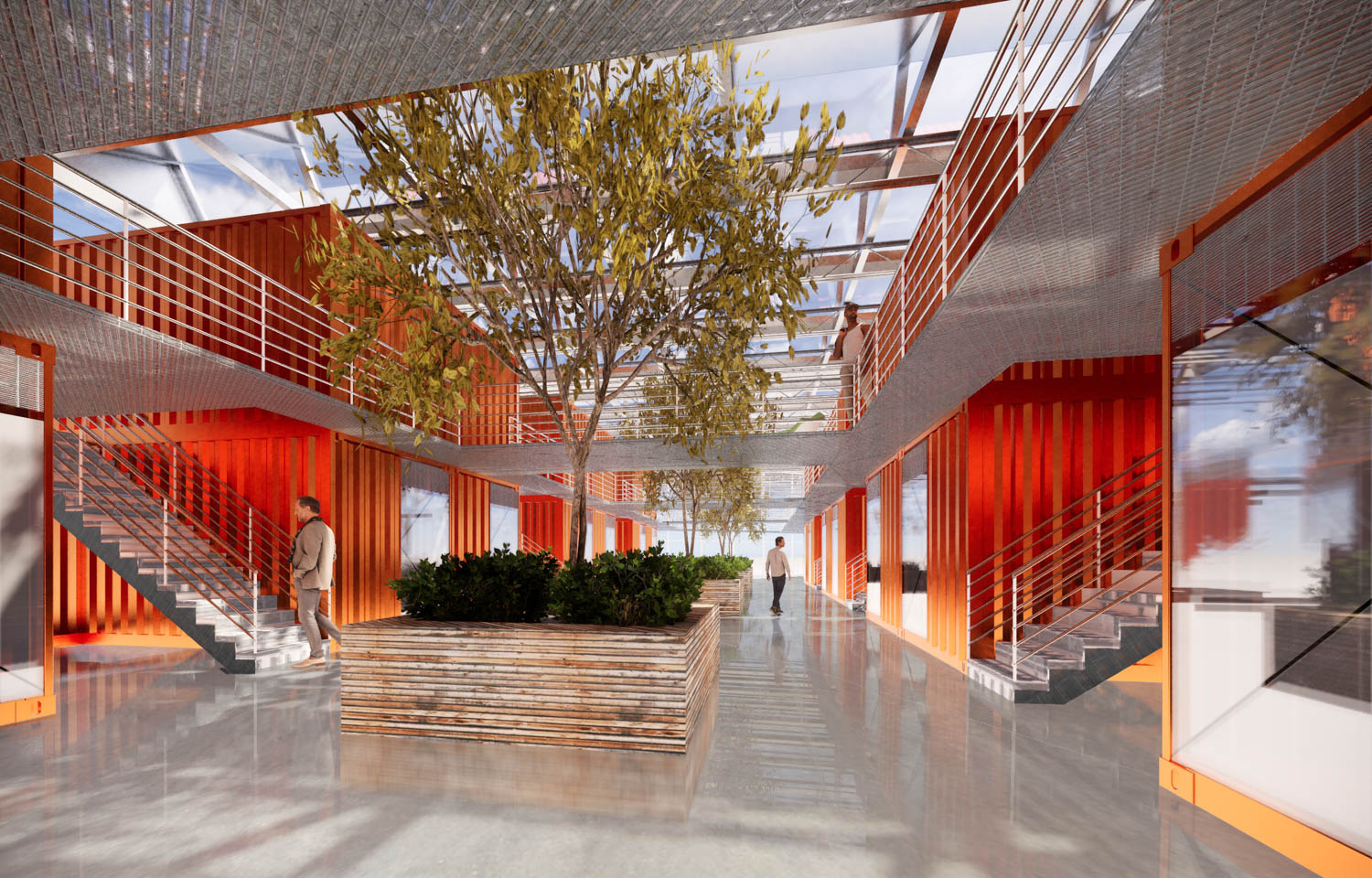
The adjacent Saint Johns Park will be enhanced with amenities as part of the project. How does the modular and prefabricated approach of the living units allow for seamless integration with these communal outdoor spaces, fostering a sense of community within the larger urban fabric?
The long neglected Saint Johns Park, backyard to the Daylight Homeless Center, presents an opportunity to invest in a community amenity and create a local hub. Cargo containers would be used as free-standing semi-permanent structures housing a weekly farmer’s market and a small performance stage. Additionally, the containers would provide secure storage for rental equipment. In addition to the containers, prefabricated kids playground equipment would be utilized while shade structures provide parents with a respite from the Texas sun.


